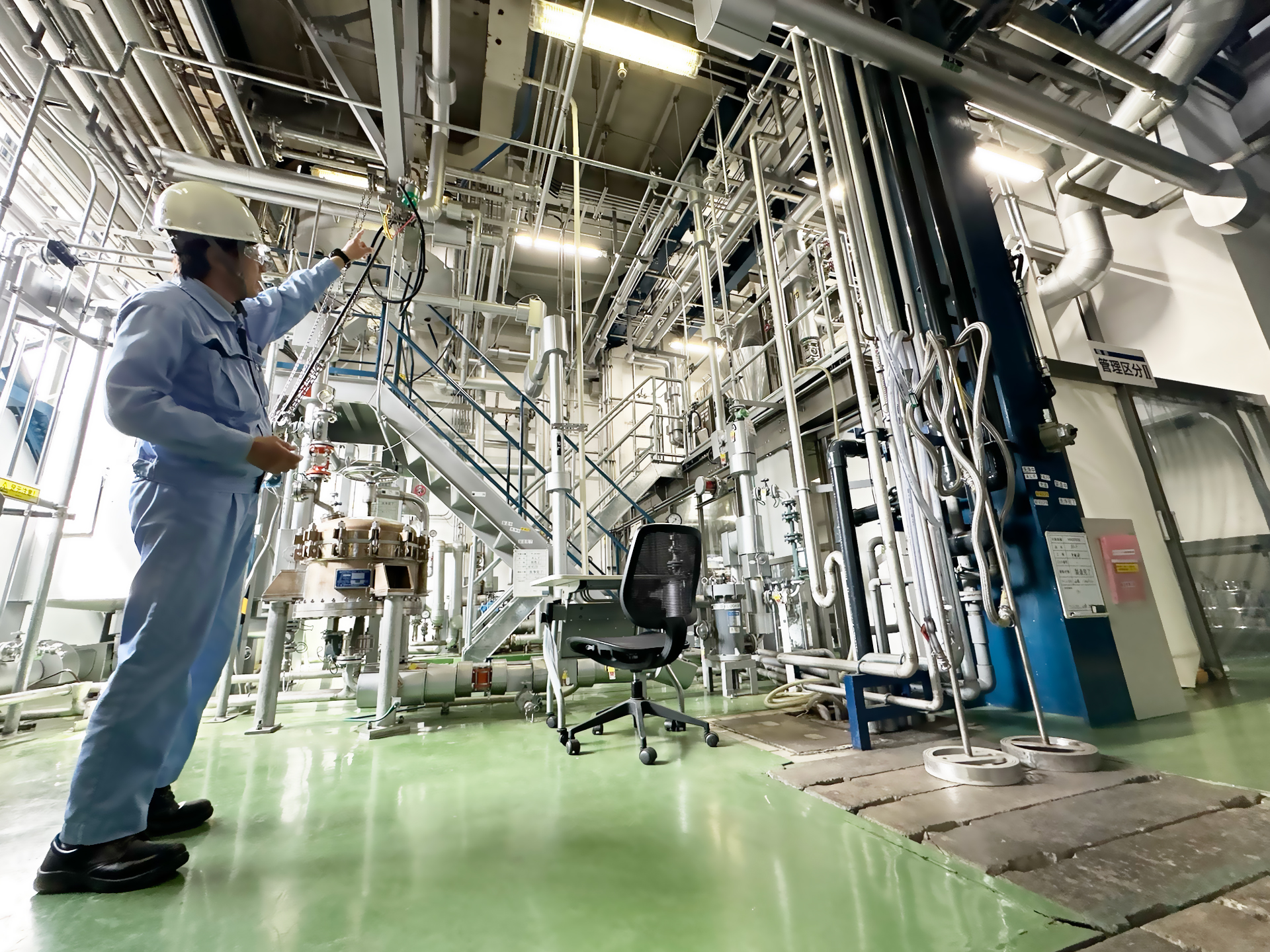
Contract Manufacturing of Pharmaceutical APIs and Intermediates
The contract manufacturing business for pharmaceutical APIs and intermediates involves pharmaceutical development companies outsourcing the manufacturing process to specialized external companies instead of owning their manufacturing facilities. This business model enables resource efficiency, cost reduction, and risk distribution in the pharmaceutical industry, which requires high capital investment, operational costs, and strict regulatory compliance.
APIs (Active Pharmaceutical Ingredients) are the main components responsible for the effect of pharmaceuticals, and intermediates are compounds produced during the manufacturing process of these APIs.
Compliance with GMP (Good Manufacturing Practice) Standards
The manufacturing of pharmaceutical APIs and intermediates is carried out under strict management systems compliant with GMP (Good Manufacturing Practice) standards. Manufacturing process development is conducted at each stage from preclinical to commercial production. The facility covers a site area of approximately 118,892 m² (about 36,000 tsubo), with a building area of about 12,000 m², production facilities of about 4,300 m², warehouse facilities of about 4,600 m², and a green area of about 52,400 m², providing ample space for future development.
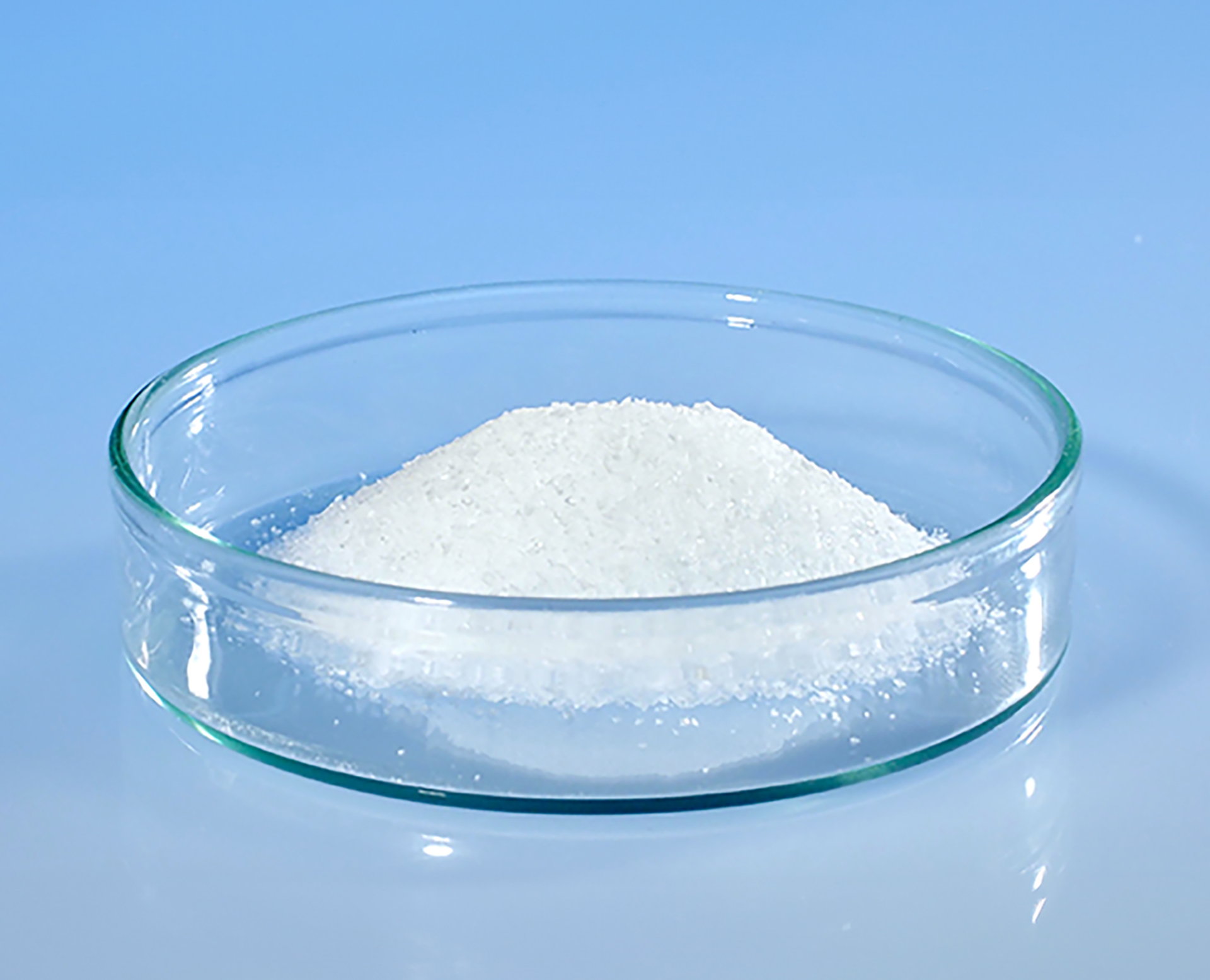
Manufacturing Track Record of Pharmaceutical Raw Materials and Intermediates
The primary focus is on manufacturing active pharmaceutical ingredients (APIs) for medical use, utilizing both chemical synthesis and biosynthesis methods. As one of the largest pharmaceutical manufacturing facilities in Japan, it houses one of the country’s largest fermentation plants, enabling large-scale pharmaceutical production with advanced biotechnology.
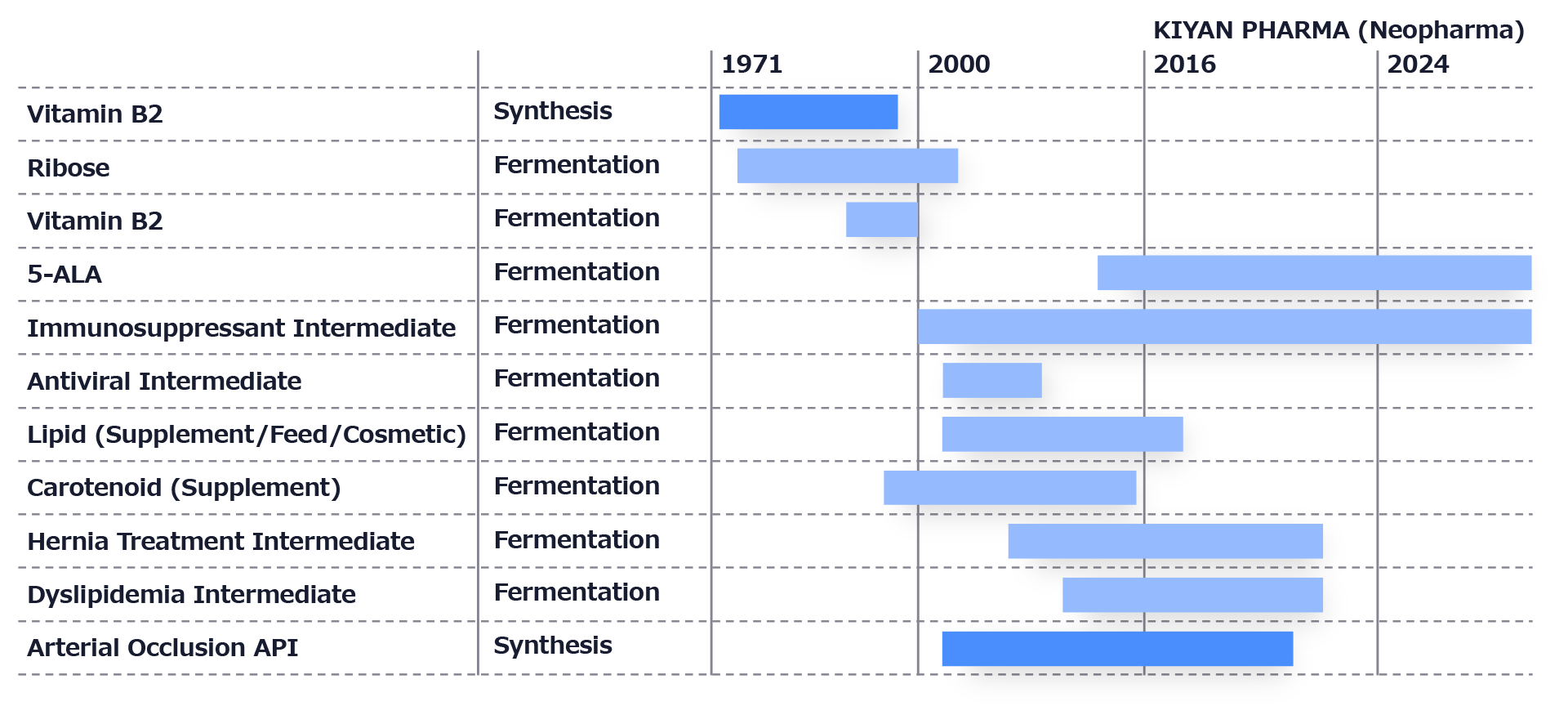
Production Facilities
Facilities are equipped for both fermentation and synthesis, enabling the production of high-value-added products through multi-stage processes.
Fermentation Facilities:
Proven capability for handling genetically modified organisms and pathogenic bacteria (Class 2).
Synthesis Facilities:
Capable of hydrogenation reactions using high-pressure gases and various chromatography/extraction/crystallization processes involving hazardous materials.
API Facilities:
Equipped with API facilities capable of producing 10-30 tons annually, with capabilities for fine pulverization of final products and ultra-fine pulverization using jet mills (Cleanroom: Class 100,000).
Pilot Facilities
- Equipped with fermentation and synthesis facilities that support pilot production from the development phase, assisting with feasibility studies.
- Offers technology transfer from lab scale, process design for small-scale production, and scale-up proposals aimed at commercial production.
- GMP-compliant manufacturing is possible, even at the pilot stage.
- Primarily focused on the production of APIs (Active Pharmaceutical Ingredients) for pharmaceuticals.
- Capable of manufacturing using both chemical synthesis and biosynthesis methods.
- Owns one of Japan’s largest fermentation facilities among pharmaceutical manufacturing plants.
- Houses one of Japan’s largest pharmaceutical production plants utilizing biotechnology.
KIYAN PHARMA Business Overview
5-ALA is manufactured to meet the quality requirements of pharmaceuticals, health foods, cosmetics, fertilizers, and animal feed.
The Fukuroi plant is expanding contract manufacturing for pharmaceutical APIs and intermediates in addition to 5-ALA production.
Supplements and skincare products containing 5-ALA support consumers’ beauty and health.
Products utilizing 5-ALA contribute to animal health and plant growth.